CC2 Phase IV Material Characterization Plan & Data
Material testing was conducted December 4, 2002 to April 11, 2005 (construction, trafficking, and the post-traffic). In this material characterization plan, laboratory and field experiments were conducted. The following sections summarize the material testing performed during construction.
PCC Design, Evaluation, and Acceptance
PCC Mix Design and Strength Testing
A total of 246 concrete beams and 246 cylinders were cast from the concrete placed in the two center-lane slabs of the three test items of the new rigid pavements. The beams and cylinders were used for laboratory strength tests. One set of samples was laboratory cured and the other set field cured. Laboratory cured samples were tested at ages 2, 5, 7, 14, 28, 56, and 90-days (Table 1). Links to download the PCC mix design data and PCC strength data can be found here.
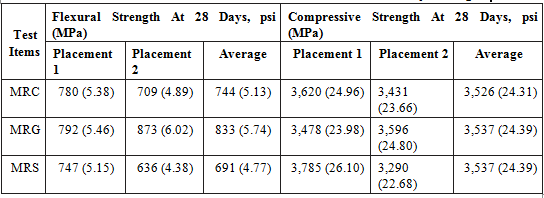
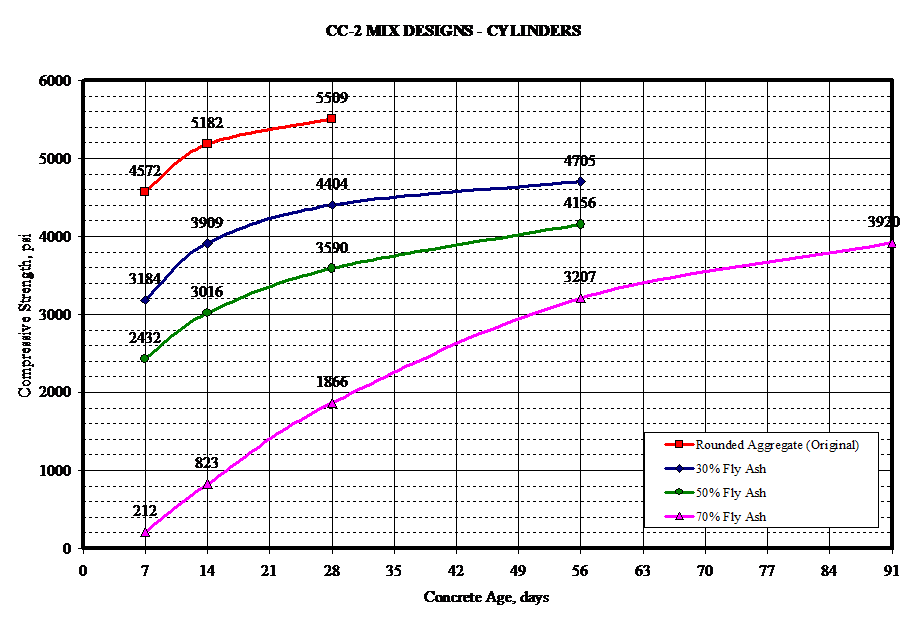
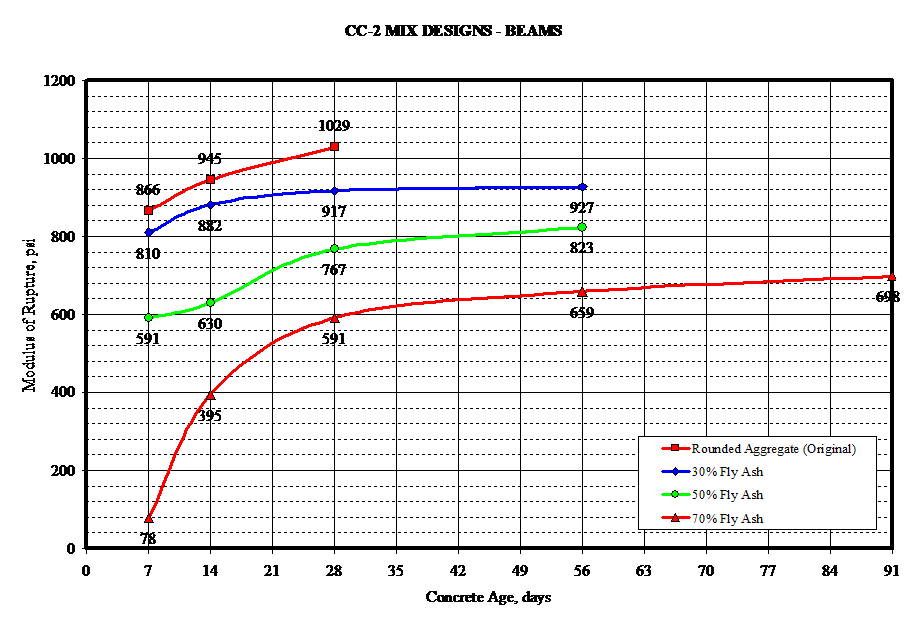
PCC Field Acceptance Testing
Slump and air content of concrete were determined on the day of placement (acceptance tests), conducted January 7 to March 2, 2004. PCC strength tests were also conducted on field cured specimens and the data can be accessed here.
Subgrade Evaluation and Acceptance
Specification for Item P‑152LM Subgrade (FOR MEDIUM STRENGTH SUBGRADE)
152LM‑3.4 Acceptance Testing for CBR. Each layer of the subgrade will be accepted when the measured CBR meets the requirements defined in Section 152LM-3.4.
Acceptance measurements will be made on each lot of completed subgrade. Each lift of subgrade, including the bottom layer, for the required length of medium strength subgrade shown on the plans, shall be divided into two (2) lots, representing material placed on the north and south sides of the test pavement centerline. Each lot area will be divided into two (2) equal areas, or sublots (See figure 1). A random location will be located in one sublot within the vehicle wheel path in accordance with procedures described in ASTM D 3665.
A corresponding location shall be established in the adjacent lot at the same station and corresponding offset. The Engineer reserves the right to perform additional CBR tests at random locations outside the vehicle wheel path to verify material quality in those areas and include these additional tests in the lot samples for acceptance evaluation.
Three (3) CBR penetrations will be made within one foot of each other at each random location in each sublot. The average of the three penetrations will be considered as an individual CBR test for that sublot provided the range in the three penetrations is less than, or equal to, 1.5. Should the range exceed 1.5, an additional penetration(s) shall be performed adjacent to the first three to test for local variability. ASTM E-178 shall be consulted to establish whether any one or more of the set of penetrations is an outlier at a significance level of 5 percent, to determine if any value(s) should be discarded when performing the acceptance computations. The average of the penetrations (or those remaining after the E-178 test for outliers), shall be averaged to establish the individual CBR test for that sublot location.
The lot shall be considered acceptable when (See Table 1):
- The range between the high and low CBR tests within a particular lot is less than or equal to 2.0 for the lot.
- The range between the high and low CBR for two contiguous side by side (i.e., north and south) sublots is 1.0.
- The difference in the average CBRs (i.e., the average CBR for the two sublots representing the particular lot) for contiguous north – south lots is equal to, or less than, 2.0.
- The average of the two lots is equal to, or less than, 2.5. For a nominal target CBR of 7, the average of the two lots material is between 5.5 and 8.0 (1.5 below target to 1.0 above target).
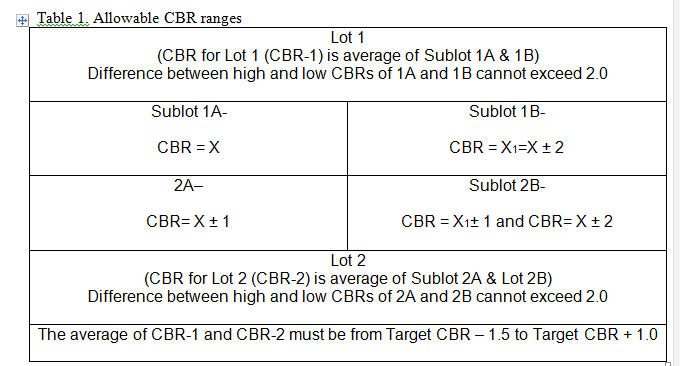
CC2 Phase IV Subgrade Quality Acceptance Test Plan
CBR tests were performed on each lift during construction of the medium-strength subgrade sections. Three penetrations were made at each test location and the mean value will be reported as the CBR value. The test locations will be selected randomly, however any test location on the north side will be mirrored on the south side or vice-versa. It is proposed that the CBR test locations preferably lie in the wheel tracks on both the sides (north side and south side). The test locations should lie between the offsets (from centerline) of –7-feet and –18-feet on the north side and 7-feet and 18-feet on the south side. At least one CBR test should be conducted in each test item for each lift. Figure 1 shows the area preferable for the CBR tests.
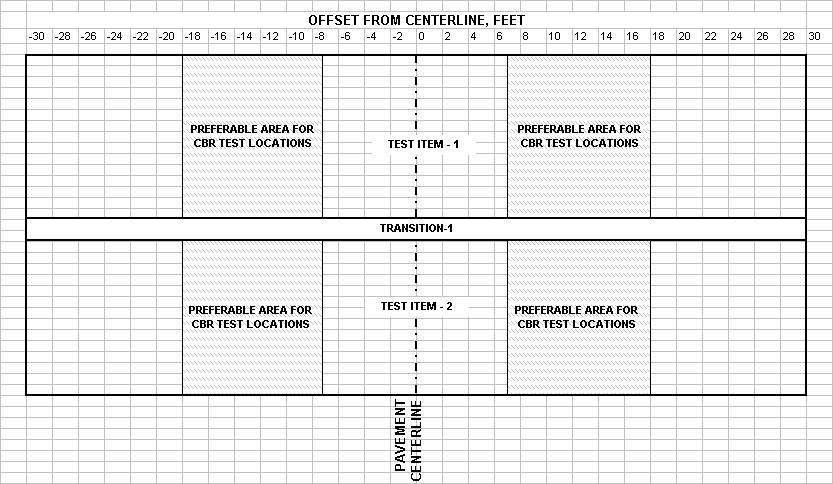
Figure 1. CBR Test Locations in Medium-Strength Subgrade
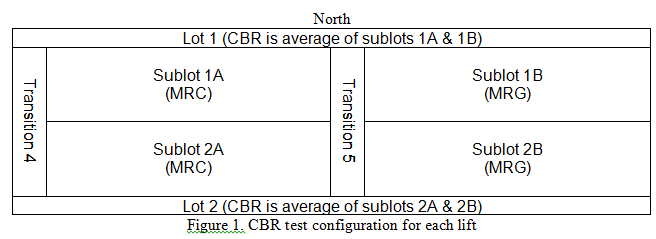
Table 1 assumes sublot 1A is the starting point. “X” is the value obtained from the average of 3 CBR penetrations. “X” (as the starting point) should be as close to the Target CBR as possible.
Subgrade material not meeting the CBR acceptance criteria shall be reported to the engineer as soon as practicable to determine a corrective course of action. In most cases, the material will be pulverized, reworked by wetting or drying, and recompacted until the CBR acceptance criteria is satisfied.
CC2 Phase IV Subgrade Quality Acceptance Test Results
The results from the CBR testing are provided in Figure 3. Click here to download (MSExcel) CC2 Test Item Materials Testing data spreadsheet including CBR test results and determination of acceptance.
Back to CC2 Phase IV Test Items