ABOUT
The FAA Airport Technology Research & Development (ATR) Branch's state-of-the-art research facilities play an important role in improving the safety, performance, and infrastructure capabilities of the national airspace system (NAS). Studies and testing conducted at these facilities support the deployment of innovative practices and technologies. ATR's laboratories and specialized equipment allow FAA to perform one-of-a-kind experiments. Most reside at the William J. Hughes Technical Center located in Atlantic City, NJ.
Learn more about what we do.
VISITORS
The William J. Hughes Technical Center for Advanced Aerospace is the aviation industry's premier research, development, engineering, testing, and evaluation facility. Visitors to the Technical Center must make prior arrangements with a FAA point of contact. Visitor information can be obtained from the security personnel in Building 320, the Security Operations Center, or from our Visitor Information webpage. Foreign visitors require special processing.
OUR RESEARCH FACILITIES
|
OUR RESEARCH EQUIPMENT
|
|
NATIONAL AIRPORT PAVEMENT TEST FACILITY (NAPTF)
At this state-of-the-art, full-scale pavement test facility, built in partnership with the Boeing Company, FAA researchers conduct realistic traffic testing on various concrete and asphalt pavement structures. Rigid and flexible pavements embedded with hundreds of sensors are subjected to simulated aircraft traffic, enabling researchers to collect high quality, accelerated test data. Major features of the facility include a fully enclosed instrumented test track that is 900-feet (274m) long by 60-feet (18m) wide, a rail-based test vehicle capable of simulating aircraft weighing up to 1.3 million pounds (589,671 kg), and 20 independently adjustable test wheels. We operate our non-destructive testing equipment, including two HWDs, the NDT Van, and other equipment when evaluating the effects of the NAPTV on test pavements. LEARN MORE
|
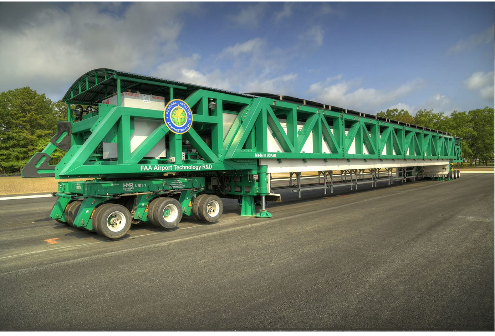 |
NATIONAL AIRPORT PAVEMENT & MATERIALS RESEARCH CENTER
The outdoor National Airport Pavement and Materials Research Center (NAPMRC) complements the work done inside ATR's National Airport Pavement Test Facility (NAPTF). This center is home to the state-of-the art Heavy Vehicle Simulator, Airfields Mark VI (HVS-A). NAPMRC is a unique research facility that allows engineers to investigate the performance of asphalt and other pavement materials outside, at very high tire pressures and aircraft wheel loads. HVS-A's automated heating system allows it to replicate the high temperatures pavements experience in summer, even during wintertime. The research performed at NAPMRC will support the integration of advanced pavement materials at airfields. New-to-airport technologies like Warm Mix Asphalt (WMA), Reclaimed Asphalt Pavement (RAP), and Stone Matrix Asphalt (SMA) are under consideration as this completes airport pavement testing. LEARN MORE
|
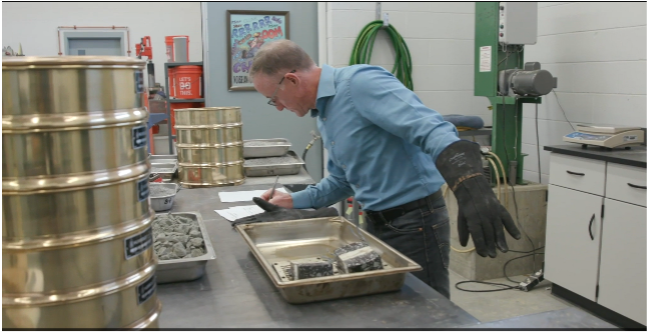 |
NEXTGEN PAVEMENT MATERIALS LABORATORY
This lab is fully equipped to test and characterize asphalt, concrete, soils, and aggregate materials used in airport pavement construction to understand the impacts on the materials in a range of scenarios. The output from the materials research program is used to update FAA standards, specifications, and guidelines on the use of conventional, sustainable, and eco-friendly materials for airport pavements. Guidelines for airport pavement material properties will be used as inputs in PANDA-AP, the FAA's advanced pavement structural analysis tool/software. LEARN MORE
|
|
AIRCRAFT RESCUE & FIRE FIGHTING RESEARCH FACILITY
This is a one-of-a-kind fire research facility. Resources include an outdoor open burn area, a fire-hardened L1011 aircraft, and a fleet of versatile test vehicles. Researchers use the facility to evaluate the effectiveness of various extinguishing agents on aircraft-related fires, such as jet fuel spills and cargo fires. LEARN MORE
|
|
AIRCRAFT RESCUE & FIRE FIGHTING TEST LABORATORY
This world-class laboratory allows FAA fire researchers to evaluate firefighting techniques and products in a controlled, environmentally-friendly way. The 2,500 square-foot (232 square-meter) facility allows for indoor testing in a building designed to remediate any environmental hazards. LEARN MORE
|
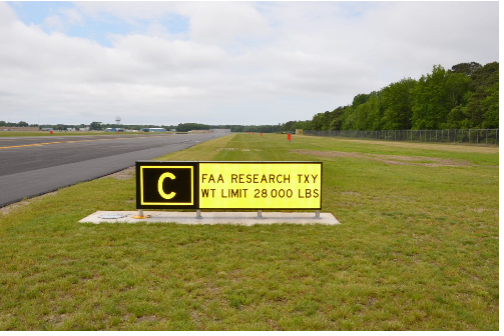 |
AIRPORT RESEARCH TAXIWAY
This taxiway opened in 2017 at Cape May County Airport (WWD) in Erma, NJ, with a full array of taxiway and runway lights, state-of-the-art lighting vault, and five unique pavement types on the taxiway. Here, researchers perform design tests and evaluation, monitoring, and reporting on advanced airport safety and pavement technologies. The taxiway provides the ability to install experimental lighting and sign configurations that can be modified and remotely monitored to meet a range of testing needs. LEARN MORE
|
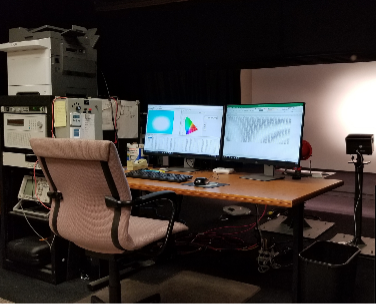 |
PHOTOMETRIC LABORATORY
FAA operates a photometric laboratory used for initial assessments of lighting fixtures for photometry and colorimetry prior to certification by an independent laboratory. FAA has specific standards for light intensity and color spectrum to make sure that lights are easy to see and operate as safely and reliably as possible.
|
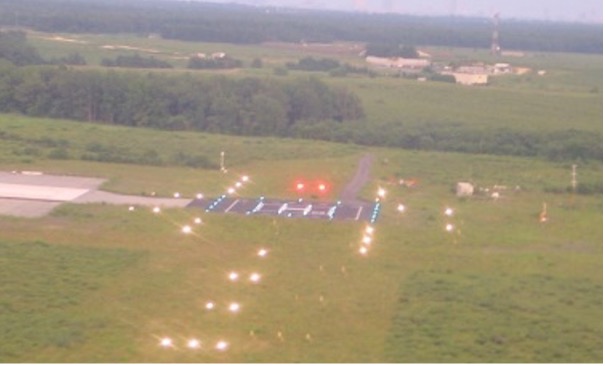 |
EXPERIMENTAL HELIPORT
This heliport platform can be reconfigured to support research and development on heliport lighting fixture types and lighting engineering standards.
|
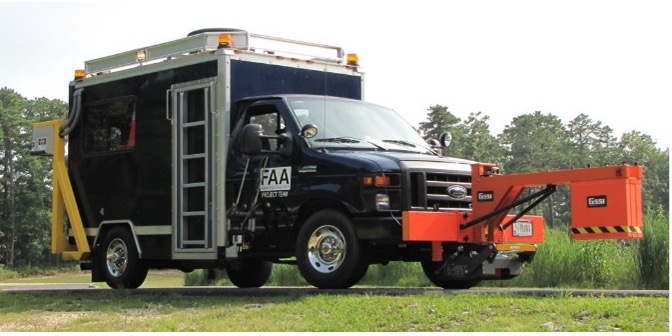 |
NON-DESTRUCTIVE TESTING (NDT) VAN
The Non-Destructive Testing Van, or NDT Van, is a mobile platform that carries multiple sets of testing equipment to evaluate and record airport pavement characteristics. The NDT Van contains three main data recording systems: 2D/3D imaging, ground penetrating radar (GPR), and an inertial profiler. The main strength of the NDT Van lies in its ability to host all of these data acquisition systems on a single platform while moving. In addition, it is capable of recording accurately at high speeds, reducing the time required to perform testing. The NDT Van is a "one-stop-shop" for the Airport Pavement section's testing needs.
Researchers use the NDT Van for pavement evaluation during pavement experiments, both at the National Airport Pavement Test Facility (NAPTF) and at airports across the nation. Researchers use the NDT Van for pavement evaluation during pavement experiences. both at the National Airport Pavement Test Facility (NAPTF) and at airports across the nation. LEARN MORE
|
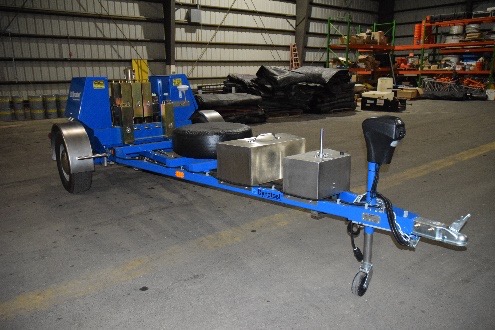 |
HEAVY WEIGHT DEFLECTOMETER (HWD)
ATR operates Heavyweight Deflectometer (HD) devices at the National Airport Pavement Test Facility, which deliver dynamic loads to the pavement surface, replicating the pressure applied by an aircraft wheel load. The HWD can accommodate up to 15 deflection measurement sensors, has a segmented loading plate, 300mm and 450mm loading plates, and 60 kips impulse load capacity.
|
Figure 1. Texas Overlay Test Specimen Figure 2. Reflective Cracking Rig |
REFLECTIVE CRACKING RIG
To convey the significance of the Reflective Cracking Rig, it is necessary to explain the scale and parameters of its function. A helpful starting point is the Texas Overlay Tester, a small-scale laboratory instrument that measures approximately 5.0 inches by 7.4 inches (12.7 cm by 18.8 cm). The Texas Overlay Tester mimics the movement of a concrete slab at the bottom of a hot mix asphalt layer, and subsequent crack growth through the asphalt, allowing researchers to evaluate the performance of asphalt mixtures.
The Reflective Cracking Rig in the NAPTF translates the testing capabilities of the Texas Overlay from the scale of inches to feet. It is the only facility in the world with the capability to conduct full-scale reflective crack testing. ATR's indoor test rig emulates the Texas Overlay test at a full-scale and simulates reflective cracking due to temperature changes of the pavement. This testing machine consists of two 15-feet by 15-feet (4.6 m by 4.6 m) concrete base slabs, one fixed and the other able to move horizontally, to simulate the opening and closing of a crack or joint. The enhanced scale of the rig allows researchers to move and test 15-foot-long concrete slabs and assess the performance of asphalt overlays on a real-world scale. LEARN MORE
|
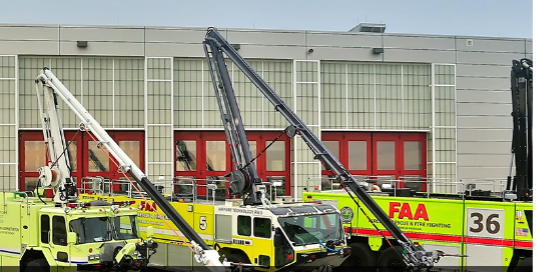 |
AIRCRAFT RESCUE & FIREFIGHTING VEHICLES
FAA’s four fire trucks are used on and offsite in various test scenarios and hold 100 to 3,000 gallons of water. Some use high reach extendable turrets (HRETs) to discharge water and foam at up to 1,200 gallons per minute. The two larger vehicles directly attack interior fires by piercing the aircraft with skin-penetrating nozzles. The newest, a 6x6 Rosenbauer Panther, tests compressed air foam systems’ functionality and performance.
|